RLE Responds To The Rise In Liquid Cooling
Article contributed by Larry Mahoney, Senior Product Manager. You can reach Larry at lmahoney@rletech.com.
RLE Tackles the Surge in Liquid Cooling with New Propylene Glycol Leak Detection Solutions
With the advent of AI and other high-density workloads in data centers, power density is increasing. To address this new cooling challenge, data center engineers are turning to liquid cooling. Key reasons for adopting liquid cooling include the demand for more efficient cooling and the need to reduce energy and water consumption. According to a report from insightaceanalytic.com, the liquid cooling market is projected to grow at a CAGR of 17.47% from 2024 to 2031.
The bottom line is that air is an inefficient cooling medium for high-power computer densities, and the application of liquid cooling is expanding rapidly.
However, with the increased use of liquid cooling in data centers, there is also a corresponding rise in the risk of damage from leaks. Leaks can occur in various components, including CDUs, cold plates, rear door heat exchangers, chilled water pipes, and overhead piping.
Common Locations for Leak Detection Sensors in the Liquid-Cooled Data Center
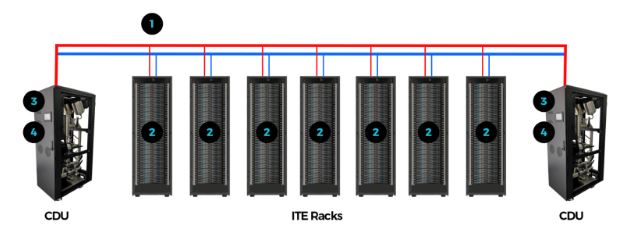
Leak Detection Sensor Layout
- Above rack rope sensor detection
- In rack rope sensor detection
- CDU point detection
- CDU rope detection
The most common cooling liquids in use today are propylene glycol-water blends. In response to the increased adoption of liquid cooling, RLE is proud to announce that our SeaHawk liquid leak detection cables are able to detect propylene glycol-water blends with up to 35% Propylene Glycol (by weight) including PG15, PG25 and PG35.
Interested in More Information?
You can confidently protect your liquid- or air-cooled data center with RLE’s SeaHawk leak detection solutions. For more information or to request a quote, visit RLE’s sensing cables product pages.
Leave a Reply